Yamaichi Electronics’ testing IC sockets, which have one of the world’s top market shares, are used in final testing in the semiconductor manufacturing process. In column Part 1, we explained what materials and technologies testing IC sockets are made from.
The contacts used in testing IC sockets play a very important role in connecting the semiconductor package and the testing board.
In this column, we will introduce what materials of the contacts used in testing IC sockets, which electrically connect the semiconductor package and the testing board, are made from.
What types of contacts are available for IC sockets for testing?
Burn-in sockets, a type of IC socket for testing developed by Yamaichi Electronics, generally use contacts processed into a leaf spring shape using press processing technology (Figure 1) to accommodate a variety of semiconductor packages.
Test sockets also need to maintain their electrical characteristics at room temperature and have repeatability characteristics to ensure frequent use in order to test many semiconductor packages in a short period of time.
Compared to burn-in sockets, which are used at high temperatures, the contacts of test sockets used at room temperature are generally set at a higher load against the semiconductor package. For this reason, a coil spring is placed inside a cylindrical contact called a probe pin (Figure 2).
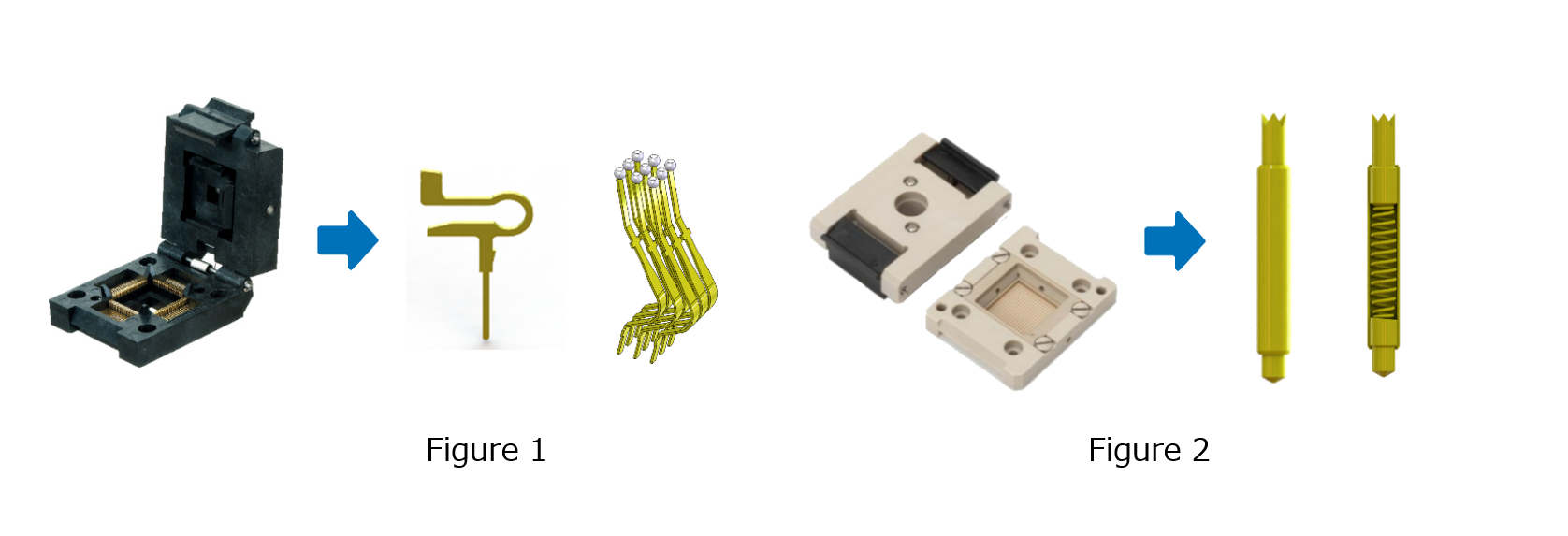
What is required for the contacts of IC sockets for testing?
The following conditions are required for the contacts of burn-in sockets and test sockets.
- Heat-resistant properties that do not deteriorate even at temperatures above 150°C, and the material must transmit heat well.
- Good electrical conductivity.
- Soft and easy to process as a base material, with good formability.
- The material must have a high surface hardness and high tensile strength.
- Good fatigue properties.
- Excellent corrosion resistance.
What is required for the contacts of IC sockets for testing?
■Materials used for burn-in socket contacts
The contacts used in Yamaichi Electronics’ burn-in sockets must be designed to be compatible with a variety of semiconductor packages. For this reason, we use materials that have excellent workability and can withstand the semiconductor package inspection environment.
Main Material Name | Main Features |
BeCu | Conducts electricity well, conducts heat well, good corrosion resistance |
*The main features of BeCu are that the base material is soft, making it easy to process, and that precipitation hardening (obtaining high hardness by heat treatment after processing the base material) allows it to achieve extremely high tensile strength.
■Materials used for test socket contacts
The contacts used in Yamaichi Electronics’ test sockets are called probe pins, and generally consist of four parts (Figure 3), each made from a different material. In particular, when used in environments close to room temperature, the probe pin contacts require high contact load and repetitive characteristics for semiconductor packages in order to test many semiconductor packages in a short period of time compared to burn-in sockets.
*Some of the probe pins we manufacture are smaller than a grain of rice. We offer a variety of material options to suit your needs and inspection environments, and can provide custom-made products to suit your needs.
Role of each part
-Plunger A: The part that contacts the semiconductor package
-Barrel: The part that stores plungers A and B and the coil spring
-Plunger B: The part that contacts the test board
-Coil spring: The part that produces the spring characteristics (load) of the probe pin
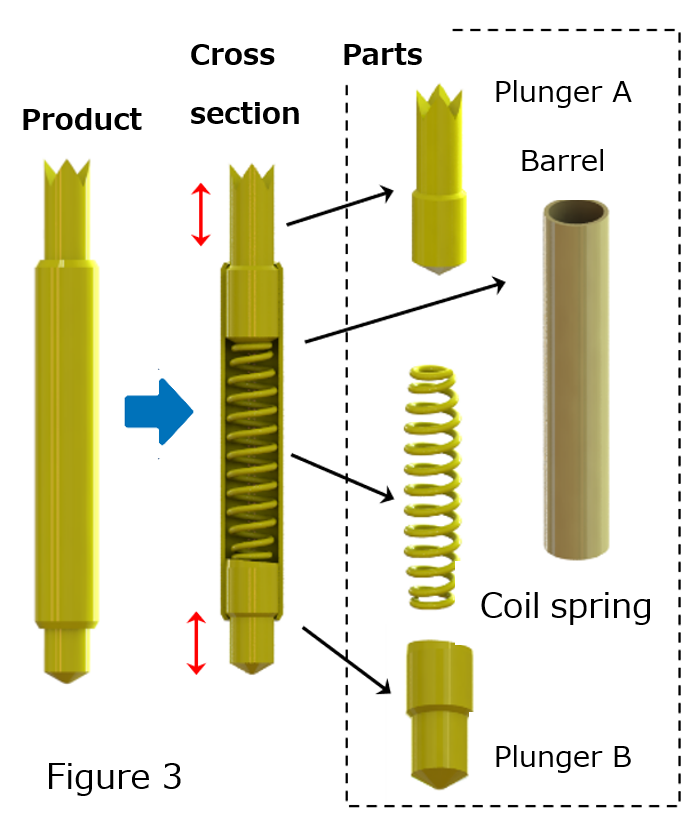
Component part | Main Material Name | Main Features |
Plunger A, B | BeCu | Easy to process and has low resistance (common material) |
SK | The surface of the material is hard and durable | |
Pd alloy | No plating required and resistant to solder transfer | |
Barrel | PB | High electrical conductivity and excellent antifriction |
Coil spring | SWP | Operating temperature is 125℃ or less |
SUS | Operating temperature is 150℃ or less |
Future trends in IC sockets and ICs for testing
Semiconductor packages are used in home appliances such as computers and smartphones, as well as in ADAS (Advanced Driver Assistance Systems), hybrid cars, and electric vehicles in the automotive field. Furthermore, as semiconductor technology for data centers and generative AI continues to develop, semiconductor packages are also expected to be highly reliable and develop rapidly, supporting the digital transformation era.
Yamaichi Electronics will respond to the market’s needs for IC sockets for testing, and will support the improvement of semiconductor quality around the world behind the scenes with its high contact technology that “reliably connects” semiconductor testing equipment and semiconductor packages.
If you are having trouble with semiconductor package testing solutions, from small-lot, high-mix burn-in sockets and test sockets to custom-made sockets for special semiconductor packages, please contact us.